Como en muchas otras situaciones en las que las características o especificaciones tienen un fuerte acento técnico, muy a menudo el cliente no solicita explícitamente la incertidumbre que requiere, sino lo hace a través de parámetros que eventualmente conducen a tal determinación.
No se conoce un método estándar, universalmente aceptado, o único para determinar la incertidumbre que el usuario requiere, pero es plausible considerar que depende del proceso en el que está inmersa la medición.
El concepto de proceso empleado aquí es tan general como la transformación de elementos de entrada en elementos de salida; puede ser un proceso de manufactura, de prestación de un servicio, administrativo, etc., y supone que existen variables asociadas al proceso, algunas de ellas representativas de la transformación y otras características del resultado final. Por lo tanto, estas variables necesitan ser medidas.
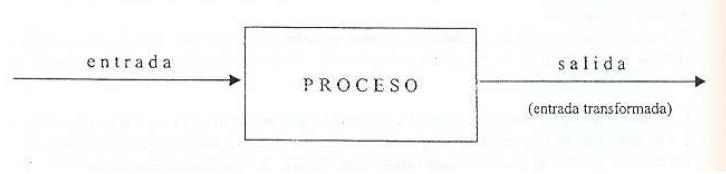
Podemos suponer que la incertidumbre requerida para medir una de las magnitudes del proceso, depende en primera instancia de: la variabilidad de esa magnitud que significa el intervalo de valores posibles, y de qué tan crítica es esa magnitud bajo medición.
El control de procesos es un tema ya muy estudiado, de modo que son de uso prácticamente universal las cartas de control como herramientas, en las que se emplean como básicos los conceptos de tolerancias, límites de control, e índices de capacidad y de habilidad del proceso (Cp y Cpk).
La figura 4 ilustra la relación entre las tolerancias y los límites de control como medidas de la variabilidad de una magnitud asociada a un proceso. Se dice que una magnitud en un proceso está bajo control cuando las mediciones de esa magnitud conforman una distribución. dada, por ejemplo, puede ser una distribución normal con una media y una desviación estándar, visto de otra manera, cuando Cp y Cpk mantienen sus valores y no se presentan contingencias que tiendan a desviarlos de esos valores.
Es útil recordar las definiciones de Cp y Cpk. en un proceso con tolerancias superior e inferior El y ES, y media en las cuales se ha asumido que los límites de control están calculados a 3 segundos.
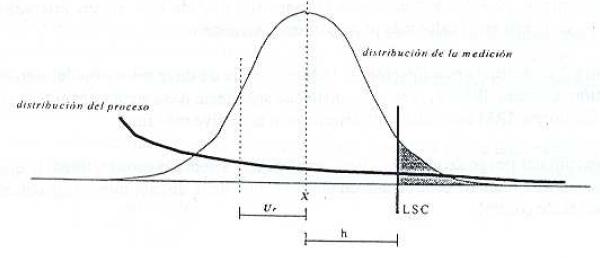
Vale la pena recordar que las especificaciones ES y Elson fijadas externamente al proceso, son requisitos para el proceso que pueden cambiarse a voluntad de quien los haya decid;do, ya sea el cliente o el responsable del proceso; y los límites de control LSC y LIG son inherentes al proceso, permanecerán fijos mientras las condiciones del proceso no cambien.
Conviene anotar que Cp mide la razón del ancho de la tolerancia a la variabilidad del proceso, esto es, qué tan holgado está el proceso respecto a las tolerancias. Por supuesto, el responsable del proceso buscará una capacidad del proceso grande. Por otro lado, mide qué tan centrada está la media del proceso respecto a la banda de tolerancia.
El responsable dormirá realmente tranquilo cuando ambas, la capacidad y la habilidad del proceso, sean grandes.
Se muestra una carta de control típica como las que se usan en una gran diversidad de industrias en todo el mundo. Sin embargo este esquema necesita ser modificado ligeramente ya que como los puntos en la carta corresponden a mediciones, debemos considerar que ya no hay seguridad absoluta en usar puntos para representarlos, y mejor debemos usar segmentos con longitud proporcional a. la incertidumbre, interpretada, recordando su definición, como el intervalo de valores que contiene al valor verdadero. De este modo, el esquema adquiere la forma mostrada en la figura 5b.
Fuente: Apuntes de Metrología de la UNIDEG